This explores our thoughts about our choice to go down the path of certified Passive House. What does it involve? Is it worth it? How much extra does it cost?
2021-01-28
By Richard Keech
What is Passive House?
Firstly, passive solar design and Passive House are not the same.
Passive solar design. Basic good home design that used configuration and orientation of the building to take proper advantage of the sun. It’s a general approach, not a specific set of rules or certification. Key elements of passive solar design in a cool or temperate climate include (in the southern hemisphere):
- facing living areas with glazing to the north to capture the winter sun;
- using fixed shade elements (eaves etc) to shade windows in summer;
- keeping the size of windows under control;
- minimising glazing to the south.
For great examples of passive solar design, see Jenny Edwards’ blog.
Passive House. Passive House, aka Passivhaus, is a rule-based certification framework for high-performance homes that originated in Europe. The key thinking behind it is that, designed right, homes should need next to zero externally applied energy to keep comfortable. The Passive House method has five key principles:
- Insulation. Very high levels of insulation;
- Glazing. Very high-performance glazing – usually triple-glazed;
- No thermal bridges. Design focussing on the details to eliminate the problem of thermal bridges in the structure;
- Air tightness. Specific very high levels of air tightness;
- Mechanical ventilation. Requires use of mechanical heat-recovery ventilators (HRV) to keep the air fresh without uncontrolled heat flow.
The best introductory text on Passive House that I’ve found is Positive Energy Homes.
Not a star rating. Certification as Passive House is binary – you get it or you don’t. There’s no equivalent of a star rating to rank degrees of performance.
Myths
Two common misunderstandings about Passive House relate to:
- The need for a heater/cooler. It’s not true that a Passive does not need a heating and/or cooling system. It’s simply the case that very little active heating and cooling is needed, but many may fit it anyway. Others choose to not have active systems, and put up with the very occasional time that is a bit too cool or warm;
- Air tightness and air quality. Some suggest that living in an airtight Passive House is going to be like living in an Esky. Not so. First, openable windows are still required. Second, the HRV can keep the air fresh 24×7 without needing to operate a window.
How we came to have a Passive House?
We didn’t start this home-build journey with any intention to build a certified Passive House. I’d previously learned about it, but wasn’t convinced it was necessary for us. During the design process, our designer, Luke Middleton, put to us that we should consider it, and that he was keen to help. Our thought process was along the lines:
- we’re already intending to build to a very high energy-performance standard;
- we liked the idea of Passive Houses – in particular the use of heat-recovery ventilators (HRVs) in Passive Houses;
- Luke suggested that the cost delta would be reasonably small, given our already-high underlying thermal-performance design.
So we did a workshop on Passive House (run by John Beurle), and checked out a couple of existing Passive Houses in Victoria:
- ‘Passive Butterfly‘ in Melbourne; and
- ‘Owl Woods‘ in Trentham.
Passive Butterfly
This is a renovation done to Passive House principles, designed by Luke Middleton. When visiting, it was great to get the detailed low down Cam Munro, the owner, on what worked, and what didn’t work.
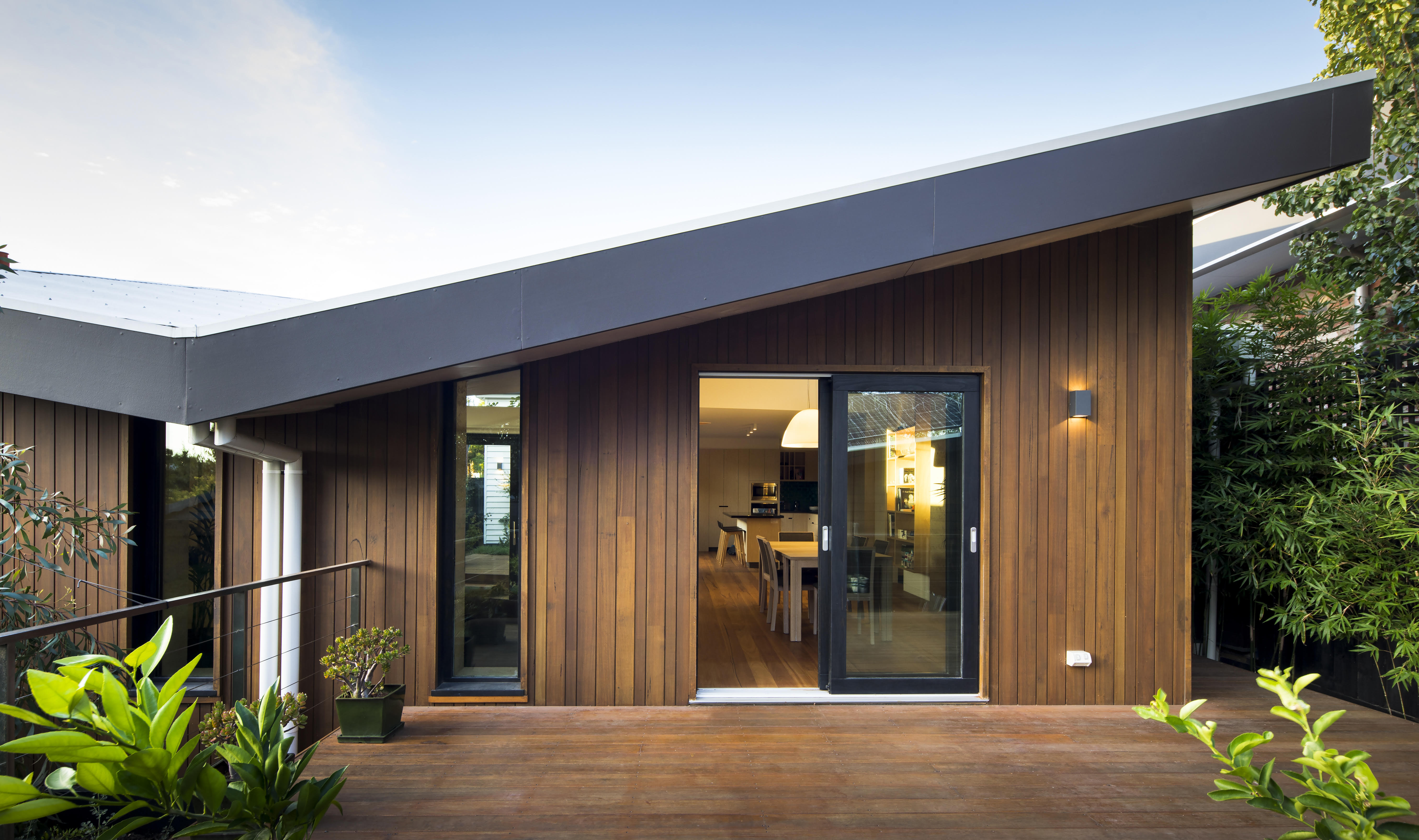
Owl Woods
This is a new certified Passive House, designed by Talina Edwards. We visited on an open day which was cold and wet. No heating was needed. We got a sense how a Passive House feels, and of the challenges and the details of what makes a Passive House.
Decisions
We liked what we saw and thought it would be fun to do this. It was apparent that a Passive House wasn’t essential. We know that it’s possible to build really comfortable passive-solar houses without the full rigour of Passive House. At the end of the day it was a decision based, not on need, but on the fun of doing something really cool and interesting, that would hopefully deliver amazing comfort and ultra-low running costs.
Raising the bar. Another attraction was the challenge of pushing the envelope. I figured that one or two super-high performance homes at The Cape would help raise the level of performance that people generally accept as non-controversial. In other words by extending the upper end of the performance scale a bit further, it becomes easier to persuade folk that the smart high-performance home designs at The Cape are OK.
Some other factors that helped sway our decision to go PH were:
- Achieving thermal performance. Our specific design brief called for very high levels of performance, so we reasoned that we were approaching PH levels in some areas anyway;
- Magic of the HRV. I was fascinated with what HRVs can do and wanted one anyway. I had a real light-bulb moment reading Positive Energy Homes when I got my head around the idea of the implications of the so-called ‘auto bypass’ (perhaps fodder for another blog);
- Keen professionals. Both our designer and our builder were really keen.
Certification or not?
Some folk going down the Passive House path opt out of the certification. There’s no problem with applying all the Passive House principles, and then not getting certification. So you hear the term ‘Passive House principles’, which is taken to mean not certified. This might be done to avoid the cost of certification. Or, it might be done because the design was intended to achieve certification but, for whatever reason, did not pass the certification test.
We’ve chose the certification route. However, the final certification is still pending.
How much extra does it cost?
This is a much harder question to answer than it would appear, because to answer it properly you have say ‘relative to what?’. When reckoning a cost delta, you have to be clear about what you’re comparing with. The other thing that needs to be explicit to answer the question properly is to know whether the Passive House build is certified or not. A common rule of thumb is that, when compared with an equivalent high-performance non-Passive House, the price difference is somewhere in the range 5% to 15%.
The extra costs to achieve Passive House certification, when comparing with the same design done to a high-performance non-Passive House would include:
- Extra design costs. This means using a certified designer, running the design through the Passive House rating framework);
- Extra build costs – structure. This mostly means costs related to the air-tight inside layer, and related costs associated with fitting the inside surface (walls and ceiling) separate from the air-tight layer;
- Extra build costs – labour. There’s more work associated with the extra attention to detail in minimising and special treatment of penetrations to the air-tight layer;
- Certified components. Passive House build is generally done using a range of components and materials that are recognised and certified for use in Passive Houses. The materials are generally very high quality, but cost a good deal more and are mostly imported from Europe;
- Extra glazing cost. Expect a Passive House to have higher-spec windows than a high-performance passive-solar build. Triple glazing is the norm for Passive House, even in Australia. This often means windows imported from Europe;
- Documentation. Achieving certification needs better record keeping by the builder and designer. This takes time, which translates to extra dollars;
- Blower-door tests. Certification requires demonstrated achievement of the air-tightness standard – not more than 0.6 air changes per hour at 50 pascals pressure (ACH50), for a new build;
- HRV. The HRV systems aren’t cheap. However, often you might find them in place of a conventional heating/cooling system, in other words there may be an avoided expense;
- Final certification. A third-party certifier is used. That costs money.
I haven’t yet arrived at an estimate of what all that comes to for our build. However, my gut feel is that it’s in the order of 5%, depending on what you include in the comparison.
Challenges
The build went quite smoothly. In regard to performance-related aspects, some of the issues that arose were:
- the normal stresses related to achieving the air-tightness level;
- faulty sliding door seal;
- issue in fitting ceiling insulation at the ridgeline.
Blower door testing / door seal
The builder budgeted for three blower-door tests. It’s normal to have two blower-door tests performed, and that’s ultimately what we did too.
Our blower door tests were done by Ash Moregensen of 3ARK.
The first test was done when the air-tight layer and glazing were all first in place, and before fitting the plaster, floor and ceiling. The idea is to catch issues with the air-tight layer before it’s covered up, so that issues can be more easily dealt with. Our first blower door test result was 0.52 ACH50.
The second test is done right at the end, to double check that the final build meets the design requirement. When our final test was done a non-trivial problem was found with the seal of the main sliding door. At first the results were a borderline fail. After some tweaking or the door, and by all accounts a lot of stress on the day, a pass result was achieved of 0.58 ACH50. I think that’s an excellent result given that it was achieved with a fixable fault in one of the most significant elements. At the time of writing the door is still to be fixed. We’re not intending to get a third blower door test, thought it might be interesting to see what the result is with a fully serviceable door seal.
Insulation issue
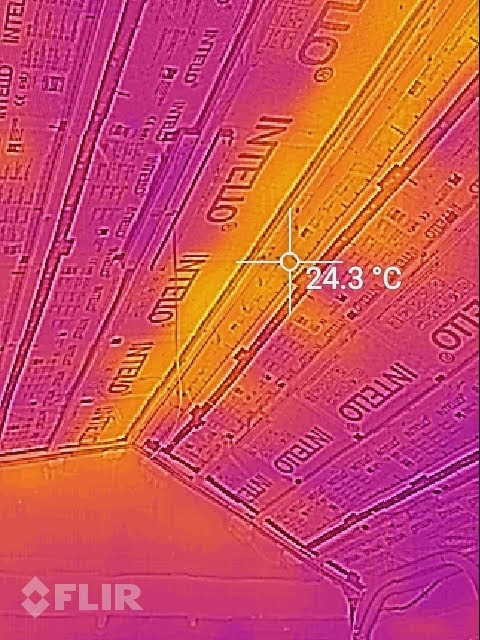
Just prior to fitting the ceiling ply in the main living area, I inspected with a thermal camera. This showed a significant problem with the fitting of the insulation along the ridgeline. This hot spot was a tell-tale indication that the insulation hadn’t been fitted properly. This required the air-tight wrap to be opened up. The problem turned out to be that the insulation batts were draped over the top of a ‘cat track’ timber element above the ridge line, leading to a significant air gap. This was plugged just in time by adding addition insulation in the air gap.
HRV – the lungs of the house
This is the control unit for the Stiebel HRV. It’s the user-facing part of, arguably, the most novel and interesting part of a Passive House – the ventilation system. In this case the controller senses air quality and regulates the operation of the unit to maintain air quality. So, the HRV unit is adaptive to its occupants. When the place is vacant, the unit will operate at a very low level, to keep energy use to a minimum. In normal daytime occupied use, the HRV steps up its rate in response to increased CO2 levels of the occupants. When necessary, the occupants can crank up the level even higher – say when you’re having a dinner party.
HRV type. Our HRV unit is a Stiebel Eltron LWZ170e Plus. It’s capable of up to 300 m3/h air flow. Nominal power consumption is 13 – 250W. Normal flow is 100 – 150 m3/h. I’m yet to measure actual power consumption, but it’s probably about 50-70W average.
Location/arrangement. We’ve put the HRV in a cupboard in the laundry. The installed arrangement of the HRV is shown below. Fresh air comes in at the top right (front), and passes through a filter box. The air passes through the heat exchanger and to the unit at the top left of the picture and is distributed to the living areas and bedrooms. Stale air is drawn from the kitchen, bathrooms, WC and utility areas and into the distribution box at the top right (rear). This passes through the HRV and then out at the bottom right of the picture.
Extra filter. The time we were designing the house was during and immediately after the extreme bushfire smoke event of early 2020. Based on that experience, we wondered how well HRVs filter smoke. Turns out they filter some, but not enough smoke. So the filter box shown in the picture (upper right) was added to give us additional options down the track to add extra filtering over and above the HRV’s existing air filters.
Shower extraction ventilation. We have HRV extraction vents over each shower. Fogging up is minimal. We normally set the HRV on high when we use the shower. However, even if we forget, then the fogging up in the shower is very minor, and clears quickly.
How’s it working?
At the time of writing, we’ve been in the house about a week and it’s all working very well. I’m particularly impressed with the operation of the HRV, which is inaudible in normal operation, except in the laundry. We haven’t experienced any extremes of temperature yet, so it’s too early to reflect on how well the it’s performing thermally. Acoustically the house is fantastic. At Cape Paterson the wind is often extreme. Also, depending on the wind etc, the noise of the surf can be pronounced. We’ve noticed that, with the windows shut, both the wind and the surf are hardly audible, making the house extremely tranquil. The structure seems really strong in the high winds. The degree of buffeting is minimal.
All up, we’re extremely happy with the Passive House-related elements of the house.